Processing Data
Brush up on conversion basics, familiarize yourself with switch terms and acronyms, and discover more about lamps and LEDs, processing and electrical ratings, and materials associated with the NKK product line.
SOLDERING & CLEANING
NKK, a pioneer in the development of washable switches, is ahead of its time as a manufacturer of process sealed switches, which are increasingly in demand because of the advancements in automated PC board processing. NKK's expansive family of washables includes toggles, rockers, pushbuttons, keypads, rotaries, and keylocks in avariety of sizes.
Over 45 years of quality design experience produced the first washable switches to satisfy the process requirements of PC board soldering and cleaning techniques. As the cutaway drawings on our Distinctive Features pages illustrate, our process compatible switches incorporate all the features necessary to accomplish washability: epoxy sealed terminals, heat resistant resins, interior rubber o-rings, seals, and sleeves, plus ultrasonic welding. The following data has been developed from a comprehensive study of test data, technical literature, and industry practice.
NON-AUTOMATED SOLDERING SPECIFICATIONS
3 seconds max. @ 350ーC max. for Hand Soldering only. Some of our switches can be damaged if these specifications are exceeded.
5 seconds max. @ 270ーC max. for Solder Pot
SUGGESTED WAVE SOLDER PROCESSING
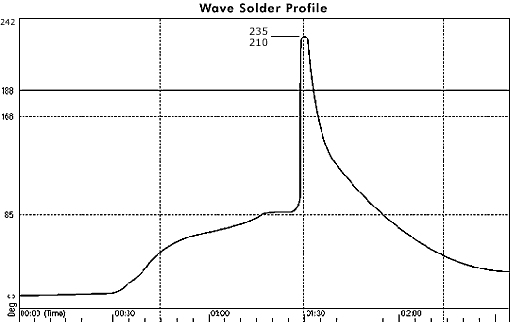
Profile
- Ramp up at 3°C per minute maximum to a soak temperature between 85°C and 104°C. Preheat and soak temperatures are critical and must be limited by some components and the glass transition temperature (Tg) of the laminate.
- Raise temperature to the Wetting Spike Zone. Peak temperature should not exceed 210°C to 235°C for 10 seconds.
-
Time above 188°C should be limited to between 20 and 40 seconds.
-
Dwell time should be as short as possible to minimize thermal damage.
-
-
The quicker the solidification, the finer the grain. The finer grain structure has better physical properties and ashiny appearance.
-
Continue cooling to 38°C.
-
Clean, if necessary.
Temperature Stabilize
To minimize the thermal shock, switches should be allowed to air cool to 38°C or to the temperature of the hand or machine wash.
Flux
NKK recommends a no-clean (low residue) flux that can be either left on the board or cleaned with a mild organic solvent.
A second choice is a synthetic flux that can be effectively removed with an alcohol based solvent.
A water soluble flux is not recommended because of the corrosive nature of the flux residue. The relative high temperature and energetic washing methods needed to ensure complete removal of all flux residues could also be hazardous to the switch.
Flux Removal
Washing should take place at a slightly elevated room temperature of between 38°C and 52°C. Spray pressure should not exceed 25 psi. Do not submerge the switch more than 2 inches. The total time that is required for removing the flux and cleaning the board should not exceed 5 minutes.
Drying
Drying time should be extended to one hour (bake) at 52°C maximum. This step will eliminate any condensation.
SUGGESTED REFLOW PROCESSING
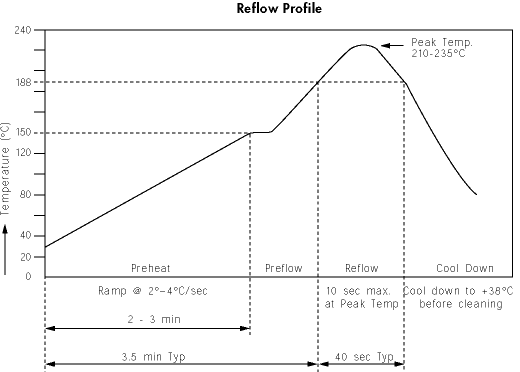
Profile
This profile is based on the use of a no-clean flux.
The boards should enter the reflow oven between 20°C and 38°C. This profile represents a "straight ramp" profile
The first ramp should be 2°C to 40°C per second to a short dwell zone of 30 to 60 seconds at approximately 150°C.
- The second ramp can be steeper to a dwell at liquid state (210°C to 235°C) for 20 to 60 seconds. Maximum timeat peak temperature should be limited to 10 seconds.Do not expose the switch to more than one pass of the profile.This profile represents a generally acceptable profile for our switches, but it is not intended for all solder paste or ovens. Some fluxes require a longer dwell at 150°C to 160°C for activation. IR ovens create larger temperature differentials on the board surface; in this case, longer times in the dwell zones allow the entire boards to achieve thermal equilibrium. Tight parameters on time and temperature must be observed to avoid component damage.